Transformer Testing Under CNAS Certification
In the core field of power equipment, the transformer is the "heart" of the power grid system.And its reliability is directly related to the safety and efficiency of energy transmission. As an industry benchmark certified by the National CNAS (China National Accreditation Service for Conformity Assessment), TSTY Testing Center has built a "zero defect" quality control system covering the entire process of design, manufacturing and delivery based on cutting-edge technology. From intelligent testing to big data analysis, each transformer must pass the rigorous test of 10+ core test items before it can be allowed to be put into use. The following is an in-depth analysis of how TSTY creates an "indestructible body" for power equipment through scientific testing.
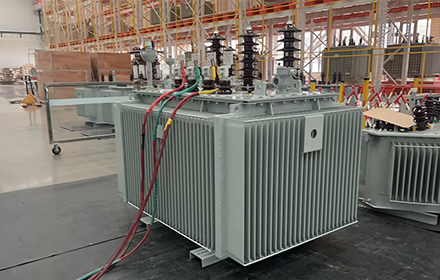
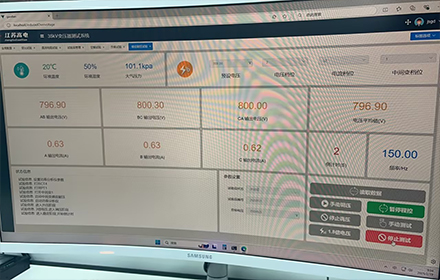
Performance Foundation Testing
1. Transformation ratio test
Use a high-precision ratio tester to verify the deviation between the winding turns ratio and the design value (the error must be ≤0.1%), ensure the accuracy of voltage conversion, and avoid harmonic distortion and energy loss.
2. DC resistance test
Use a four-wire microohmmeter to measure the DC resistance difference of the winding (three-phase imbalance <2%), locate potential poor contact or material defects, and eliminate the risk of local overheating.
3. No-load and load loss test
Simulate actual working conditions, quantify transformer no-load current (reflecting the magnetization performance of the iron core) and load loss (characterizing the conductive efficiency of the copper wire), and provide core data support for energy efficiency rating certification (such as GB 20052).
Extreme Environment Simulation Verification
1. Lightning impulse and power frequency withstand voltage test
Apply standard lightning waveform (1.2/50μs) impulse voltage with a peak value of 3-5 times the rated voltage to test the lightning resistance of the insulation system.
In the power frequency withstand voltage test, 50Hz AC high voltage is applied for 1 minute to detect whether the main insulation is broken down or flashed.
2. Induction withstand voltage test
Through 2 times the rated voltage and 100-400Hz high-frequency excitation, the test focuses on the insulation strength between layers and turns, accurately exposing winding process defects.
3. Short-circuit impedance test
Simulate a sudden short-circuit fault and measure the impedance percentage (deviation must be <5%) to ensure that the system protection device responds sensitively and prevent equipment burning accidents.
Durability Test
1. Temperature rise test
Under full load operation, the infrared thermal imager monitors the temperature rise of the winding and oil in real time (limit value: top oil 55K, winding 65K) to verify the effectiveness of the heat dissipation design.
2. Comprehensive analysis of insulating oil
Perform breakdown voltage (≥30kV), dielectric loss factor (tanδ<0.5%), trace water content (≤15ppm) and chromatographic detection (DGA) to predict potential faults.
3. Insulation resistance and polarization index
Use a 5000V megohmmeter to measure the insulation resistance of the winding to ground (>10GΩ) and the 10-minute/1-minute resistance ratio (PI>2.0) to evaluate the insulation aging status.
Choose TSTY, Choose Quality Transformers
TSTY relies on cutting-edge technology from intelligent detection to data analysis to ensure that every manufacturing detail is extremely accurate. Before the product is delivered, each transformer must undergo rigorous testing here. At TSTY, testing is not a simple "qualified" or "unqualified" judgment, but a multi-dimensional quality coordinate system is built through 12 precision tests. From nano-level insulation defect capture to million-volt extreme voltage challenges, we use science as a ruler and data as evidence to make every transformer a "power guard" that can stand the test of time. Choose TSTY, let us work together to let green electricity change the world.
TAG:   transformer testing CNAS TSTY Transformer