What Is Transformer Production Process?
Oil-immersed transformers are widely popular for their wide application and wide range of capacity. The manufacturing process of transformers is relatively complicated. The following is an introduction to the transformer production process by TSTY transformer manufacturer.
Transformer production process
Core production: Core production is the first process in the production of transformers. We use fully automatic equipment to produce cores, with a high degree of automation of 95%, which not only improves efficiency but also ensures product consistency and accuracy. Our core material is made of high-quality silicon steel sheets with high magnetic orientation to ensure electromagnetic performance.
Raw material testing: In the transformer manufacturing process, raw material testing is a key link to ensure product quality and performance. Raw material testing includes testing copper foil, copper wire, insulating cardboard, porcelain bottles, conductive rods, tap switches, etc. We will conduct strict testing on raw materials to ensure that the transformer meets quality standards during the manufacturing process and improve the overall performance and reliability of the transformer.
Insulation production: The quality and performance of transformer insulation are crucial to the safe operation of the transformer. The insulation material is cut into the required shape and size according to the design. Then, the cut insulation parts are ensured, rounded, moisture-proof and other steps. After the production is completed, it needs to be inspected to ensure that there is no damage, delamination and cracks, no metal dust and other foreign matter, so as to ensure the quality and performance of the insulation.
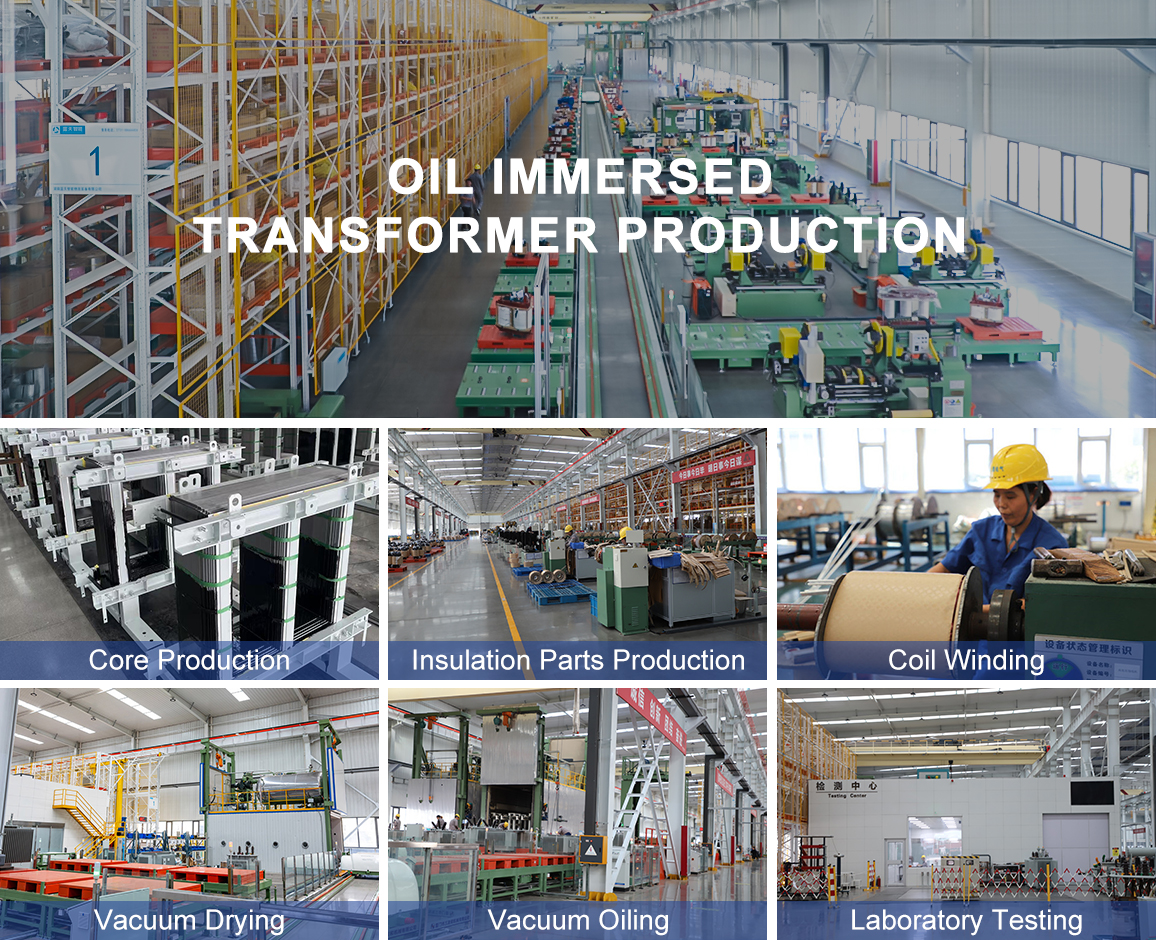
Winding: We actively introduce cutting-edge automatic winding technology to make the winding process more accurate and efficient. During the winding process, the tension and angle can be accurately controlled, the wire diameter, number of turns and tension can be finely adjusted, the movement of the motor can be accurately controlled, and the winding speed and tension can be accurately matched. These not only improve the accuracy of winding, but also greatly improve production efficiency.
Suiting process: During the suiting process, we use a paper tube of a certain thickness to protect the iron core to avoid damage to the coil during the suiting process. The overlapping part of the paper tube is designed to be long enough to ensure the stability and strength of the entire structure. We ensure that the coil fits tightly with the iron core, which is the key to maintaining the stability of the transformer during operation.
Welding process: We use advanced automated welding equipment to weld high and low voltage leads. These equipment can accurately control the temperature and time during the welding process to ensure that the welding points are firm and reliable. After the welding is completed, we will conduct strict quality inspections. Through the automated control system, key parameters such as temperature, pressure and speed during the welding process are monitored in real time.
Vacuum drying: This step ensures that the insulation material and coil are thoroughly dried to ensure the safety and durability of the transformer. The technology matched with the vacuum drying equipment we use uses a vacuum environment to promote uniform heat transfer. Rapid dehumidification protects the insulation material from high temperature damage, thereby improving the consistency and reliability of the transformer.
Vacuum oil filling: The vacuum oil filling technology we use ensures that there are no air bubbles inside the transformer, improving the durability and quality of the product. The transformer oil used by TSTY is transparent, free of suspended matter and mechanical impurities, and meets national standards. Our production line uses automated control to ensure that the oil filling process of each transformer is accurate and correct to meet the needs of large-scale production.
Laboratory testing: TSTY has established an advanced testing center accredited by the national CNAS laboratory. Every transformer manufactured by TSTY will undergo a series of rigorous tests, covering lightning impulse, temperature rise, oil test, insulation resistance, DC resistance, transformation ratio, no-load loss, no-load current, load loss, short-circuit impedance, inductive withstand voltage and power frequency withstand voltage test, etc., to ensure that it can operate stably in any environment.